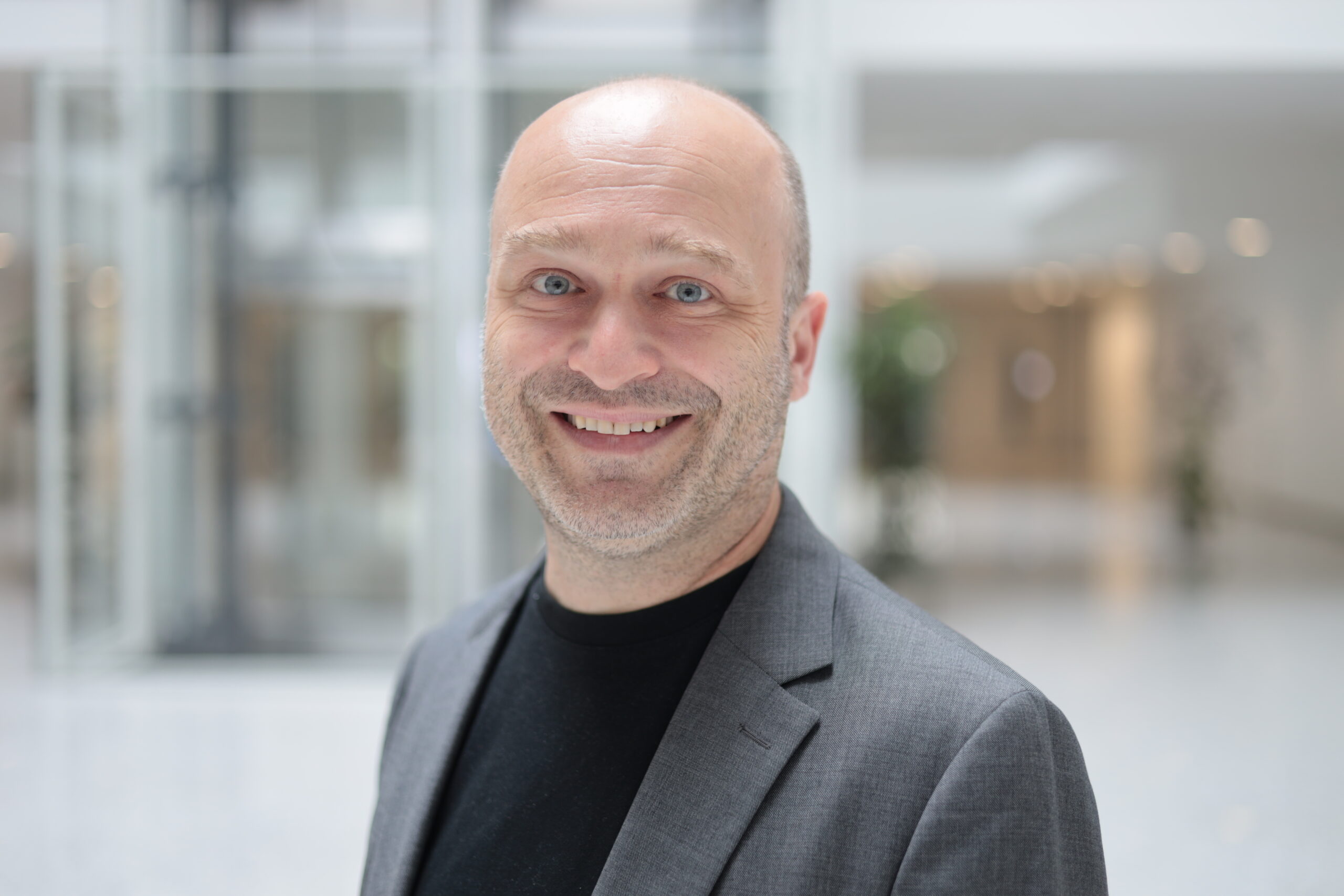
Welcome to this interesting interview about Virtual PLCnext Control with Dr. Tobias Frank (Vice President Automation Systems of Phoenix Contact GmbH & Co. KG) and the magazine Computer&Automation International (edition January 2025).
Virtualization is making great strides in automation technology. Phoenix Contact is now launching its proven PLCnext Control in a virtual version. Listen to Dr. Tobias Frank in this interview about the advantages of Virtual PLCnext Control.
C&A: How does Phoenix Contact see the future of the classic PLC compared to virtual controllers? Is a long-term shift to fully virtualized solutions planned?
Frank: The Virtual PLCnext Control is a supplement to our hardwarebased PLCnext Controls. In applications where cycle times of less than one millisecond are required, physical controllers are currently still the preferred choice. We see their use in applications where an industrial PC or IT-based hardware is already available. Here, a physical PLC can simply be dispensed with. AGVs are an example of this. Furthermore, the field of application ranges from the edge to the cloud. We offer Virtual PLCnext Control as an option for our industrial PC portfolio. However, it is also available as a pure software solution. The constant innovation in the embedded area and the support of virtualization methods in cost-effective CPUs will lead to virtualized solutions penetrating further and further into the field level over time.
C&A: Is ‚Virtual PLCnext Control‘ already being used by customers? If so, what experiences have you had?
Frank: The Virtual PLCnext Control is being used by several customers in pilot applications. During this pilot phase, we incorporated the feedback directly into the product. The experience: it works.
C&A: To what extent does ‚Virtual PLCnext Control‘ differ in terms of performance and maintenance whether it is installed in the cloud, on a Linux-based server (edge PC) or on an industrial PC (on-site)?
Frank: The performance of Virtual PLCnext Control depends solely on the complexity of the application and the available hardware resources. When designing the application, attention must of course be paid to the determinism required for communication with the controlled devices, i.e. on the fieldbus. The more ‚network‘ there is between the virtual instance and the field device, the more latency and jitter will occur. It makes a significant difference to data transmission whether the virtual instance is running on an industrial PC directly on the machine, on the edge PC or in the cloud. From a technical perspective, there are no differences when it comes to deploying Virtual PLCnext Control. Our solution consists of a lightweight OCI container. OCI is an open container format that is compatible with the Docker ecosystem, among others. In other words, the Virtual PLCnext Control can work in any Docker environment, but is not limited to it. Organizationally, the situation is different. The discussions as to whether responsibility lies with the operator‘s OT or IT have long since begun.
C&A: What license models and capacities does Phoenix Contact offer for ‚Virtual PLCnext Control‘, and how is scalability guaranteed for small and large automation projects?
Frank: We provide the Virtual PLCnext Control as a subscription model or ‚classic‘ software license. The scope of services is scaled in three stages. This includes functions and quantity structures. The performance is identical in all levels and achieves a cycle time of up to one millisecond. Virtual PLCnext Control integrates seamlessly into the existing PLCnext Technology ecosystem. This means that additional functions can be loaded via PLCnext Store.
C&A: What special security functions and protective measures are provided for the virtual PLC solution to prevent tampering or cyber attacks?
Frank: Our hardware-based PLCnext Controls are already certified in accordance with IEC 62443 and have a high level of security. The virtual PLCnext Control is based on the identical technology. This means that all known and proven security mechanisms are also included in the virtual version. Regular security updates ensure that known vulnerabilities are quickly rectified and the system is kept up to date. Regardless of which PLCnext Control variant the user chooses – physical or virtual – they are ideally positioned for the Cyber Resilience Act. Phoenix Contact also offers services in the area of cybersecurity.
C&A: How are IT and OT teams trained and supported in the introduction and use of virtual control to ensure smooth commissioning and maintenance?
Frank: The virtualization of the control level is a logical step in IT/OT convergence. IT teams are required to acquire OT know-how and understand the special requirements of OT. The same applies vice versa. We use a multi-stage concept to introduce IT and OT users to the topic of Virtual PLCnext Control. We offer basic training on PLCnext Technology as well as advanced workshops on virtualization and virtual control. This is supplemented by video tutorials, best practice reports and sample applications in our PLCnext Community.
“The virtualization of the control level is a logical step in IT/OT convergence” (Dr. Tobias Frank)
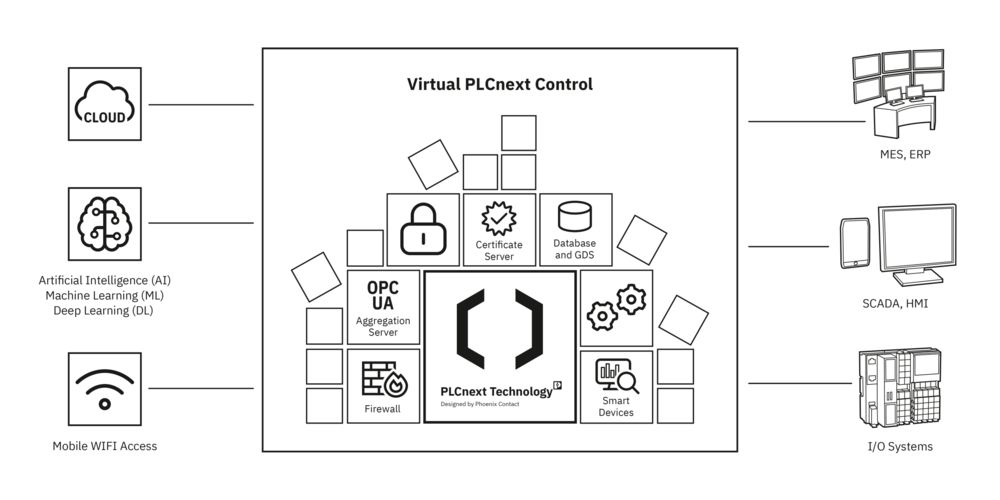
Thanks to container technology and the resulting increasing hardware independence, Virtual PLCnext Control can benefit directly from the interfaces, functions, and performance of the target hardware. For example, connection to the system network via Wi-Fi and deep learning by using the target hardware performance are possible. Furthermore, Virtual PLCnext Control provides familiar functions from the PLCnext Control world, such as the firewall, the certificate server, fieldbus connections, and even database functions. OPC&UA and PROFINET can be used to communicate with the SCADA and control system as well as with the I/O fieldbus level.
Did you like this interview about Virtual PLCnext Control? Read more about the Virtual PLCnext Control on this page.
We invite you to read this interview directly in the E-Paper of Computer&Automation International (the article is on page 18-19).