A digital twin helps to stay in charge – of a beehive or production process
The idea
Many beekeepers operate several beehives at various locations simultaneously. It is often difficult for them to differentiate, which bee-colony is at what stage of their life cycle at the moment. A great way to monitor and visualize each hive would be to create digital twins of them. This would not only enable the beekeeper to have a concise overview of all current information regarding a specific beehive, but also to keep track of and control all important processes.
From building the beehive to stacking it with food to breeding the next generation bees to harvesting the honey – a digital twin helps to stay in charge of any step along the way.
The solution
The Mittelstand-Digital Zentrum Hannover (center for digitalizing medium-sized business Hanover, Germany) has designed and created a digital twin of the beehive set up by Phoenix Contact as part of the global Beehyve Campaign by PLCnext Technology. Their digital model of the actual hive contains information on all hardware and software elements that make up the hive, an interface to connect all sensors and measurement devices that monitor the hive, and a standardized log of the processes that occur during a regular year within any given bee colony.
The digitalization experts at the Mittelstand-Digital Zentrum have also created a digital twin of the honey-making process, which enables the beekeeper to keep track of where each jar of honey originates and even how much CO2 emissions it creates until reaching its customer. With this holistic tool, merely every single aspect of the beehive and honey-harvesting process can now be visualized and controlled via just one interface – the digital twin.
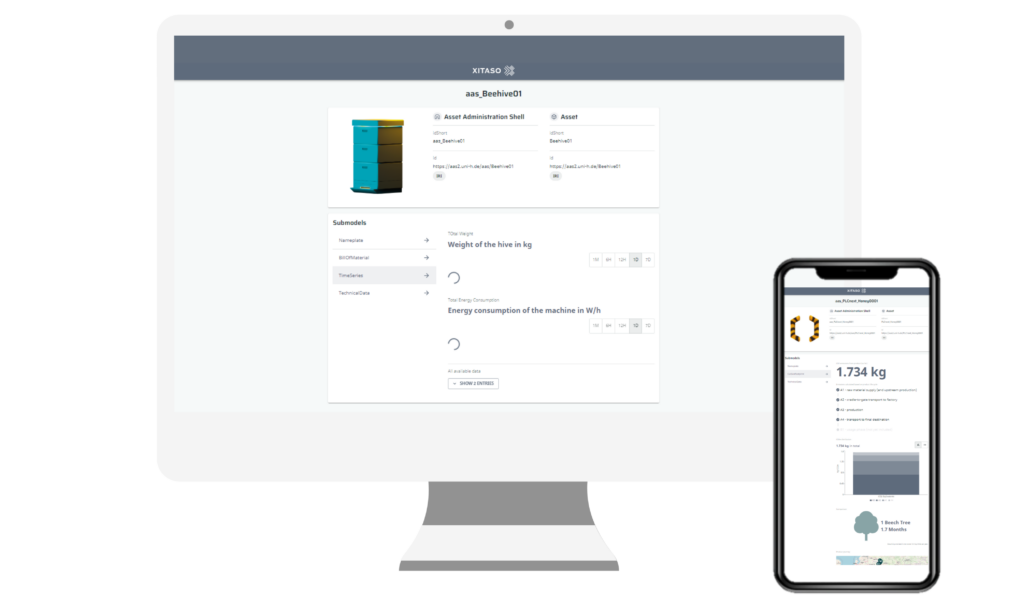
Adaption to industrial world
It doesn’t take all that much imagination to think of areas in the industrial world, where the implementation of a digital twin would help simplify, steer, and optimize merely any sort of process. By applying digital twinning, standardized protocols or workflows could be easily adapted to many different production sites. By streamlining all relevant data concerning various variables of a manufacturing process, the process itself will be much easier to manage.
Digital twins are a great way of simplifying complex procedures and thus optimizing the control over these procedures. In modern industrial settings this holds true especially when operating with open-code and vendor-neutral systems, like the one presented by the Mittelstand-Digital Zentrum, which runs on PLCnext Technology.
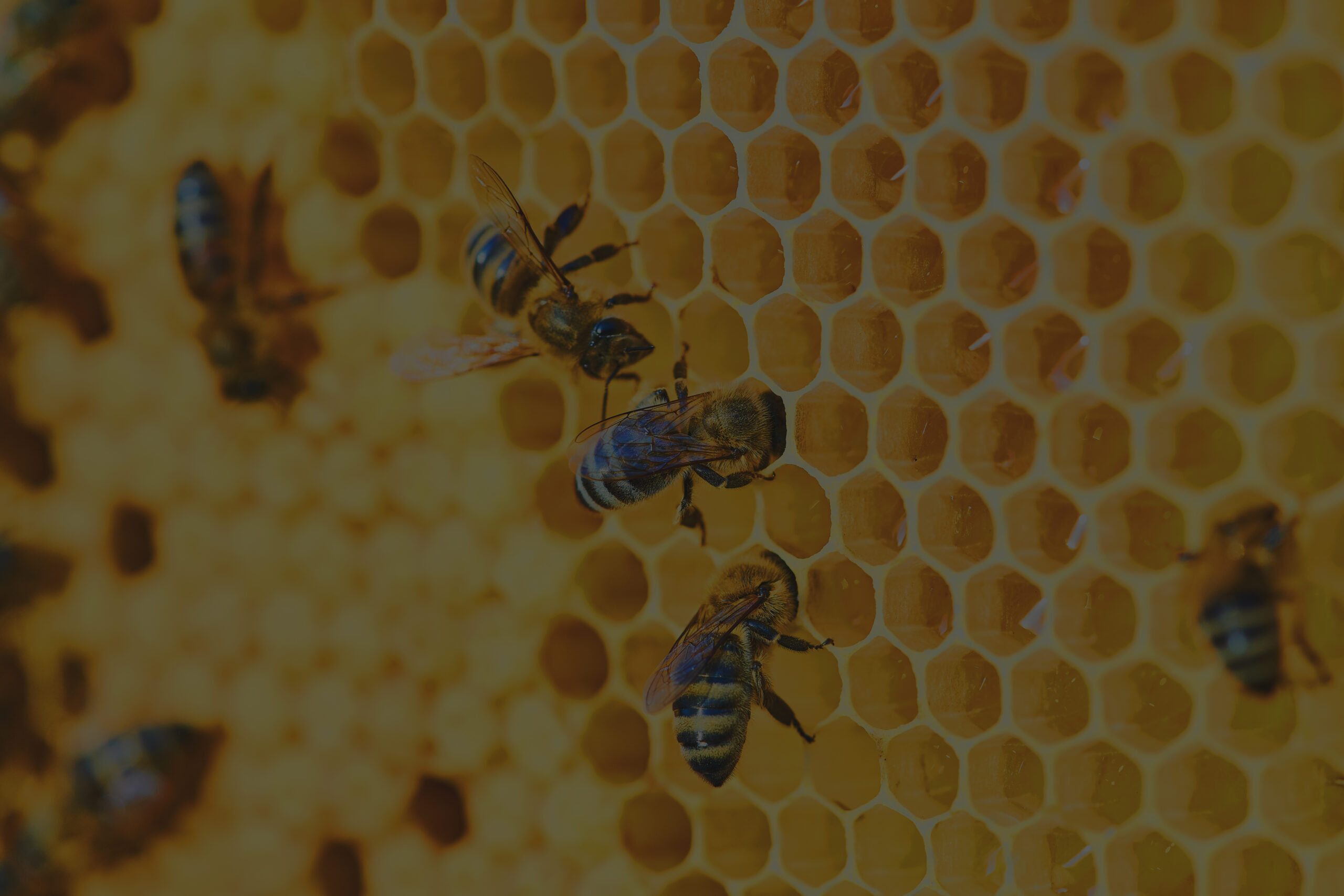