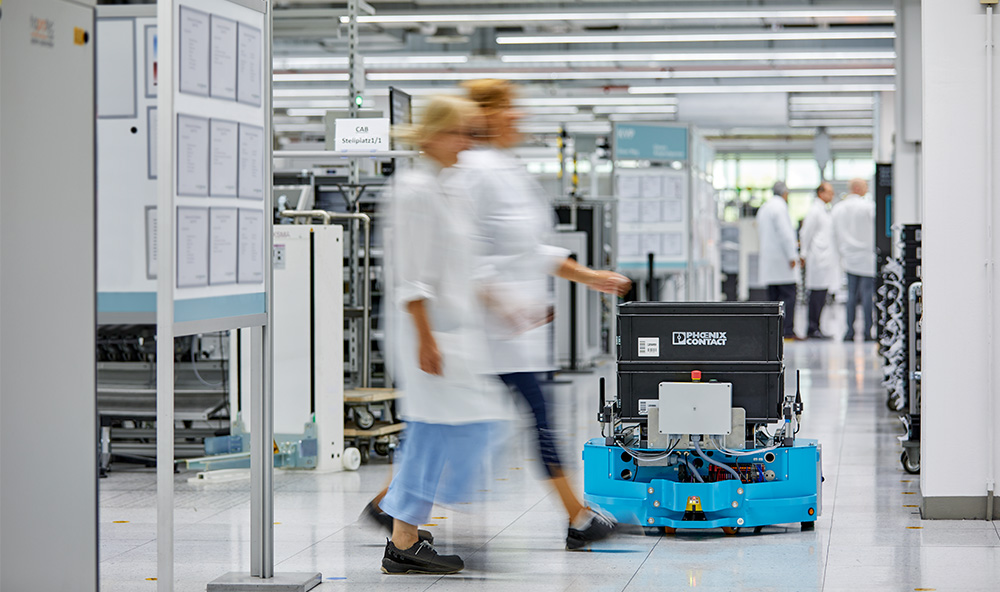
Monday morning, production hall G31 at Phoenix Contact in Blomberg: The assembly workers on the early shift have just occupied their stations, and the material is already whirring through the aisles. Three transport robots are moving well-filled Kanban containers to the machines and systems. At first glance, the vehicles could be described as sturdy metal racks on battery-powered wheels. At a maximum speed of 1.2 m/s, they take the shortest route to their destination. If an employee gets in their way, they brake directly and reliably continue their journey as soon as the path is clear.
Until the vehicles could integrate so well into the production processes, Phoenix Contact has put a lot of know-how into optimization since 2020, using its own hardware and software for automation.
Companies around the world are using automated guided vehicles and autonomous mobile robots – primarily to automate manufacturing and logistics processes. In addition to the quite established logistics application (for example, in high-bay warehouses), these systems are also increasingly optimizing production supply. This is also the case in Phoenix Contact’s production. There, the AGVs transport the material from the automatic small parts warehouse to the production machines and pick up the finished goods from there again. The entire process is automated and fully integrated into the digital processes and IT systems. Material is automatically retrieved as needed, collected by the autonomous vehicles, and brought to the machine that requested it for the next order.
In this way, the AGVs significantly reduce the delivery times for the material and reduce circulating stocks in production. This means, for example, that more usable production space is available. In addition, employee ergonomics are improved because material is delivered to transfer stations at a user-friendly height, eliminating a lot of bending and lifting.
Experience shows that three issues are particularly challenging when planning and implementing an automated guided vehicle system:
- path planning and navigation to a specific destination,
- the avoidance of collisions and other accidents, and
- protection against cyber attacks.
Find out below how these challenges were solved at Phoenix Contact.
Everything in it: Control, Safety, Security, Navigation, Electrification, Communication and Energy
To enable them to perform their tasks autonomously, the driverless transport systems were equipped with extensive intelligent technology and sensors. In addition to controlling the load transfer functions, the focus was on the safety of the people in the production area. In addition, each vehicle must be able to navigate from source to sink with pinpoint accuracy – and the battery should be charged at the appropriate time. For these functions, Phoenix Contact used components and systems from its own portfolio that were specially designed for this area.
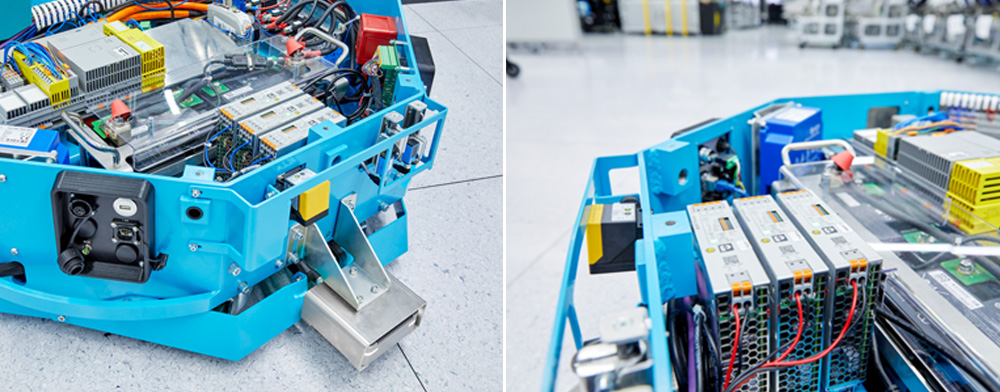
Anyone who wants to take a holistic view of the automation technology of an AGV should include seven areas: Control, Safety, Security, Navigation, Electrification, Communication and Energy. With this division, the project team at Phoenix Contact has also developed the individual topics in a structured and compatible manner – all based on the open ecosystem PLCnext Technology.
Control: The remote I/O system
From the point of view of a classic control system, real-time relevant tasks are implemented in the AGV. A powerful remote I/O system for data and signal traffic must therefore be connected to the PLCnext Control. The project team decided on the new I/O modules of the Axioline Smart Elements series. The compact, robust and flexible modules save up to 75 percent space in the control cabinet compared to conventional I/O systems. The vibrations that occur in any AGV have no negative impact on the hardware, even in continuous operation.
The Axioline Smart Elements I/O modules enable the coupling of I/O signals for controlling the vehicle. Signaling and command devices (for example lamps and pushbuttons) are also connected to the system. The safe input and output signals, such as emergency stop buttons or the brakes, have been integrated into the control system using the safe Axioline I/O modules. Via Profisafe protocol, the safe data can be transferred to the safety expansion module (AXC F XT SPLC 1000) connected to the left of the PLCnext Control and processed there. The comprehensive range of Axioline I/O modules covers the most important serial protocols, for example CAN, RS422 and RS485. Function blocks freely available on the PLCnext Store digital marketplace simplify the integration of these protocols into the application project. The Axioline CAN module is used to communicate with two DC servo drives for the wheels. For the journey to the destination, the PLCnext Control transfers the setpoints transferred by the navigation unit to the drives according to the CAN-open protocol.
Safety: Reliable accident protection
The automated guided vehicles act together with the employees, which is why the AGVs must meet strict safety features, such as the reliable detection of (sudden) obstacles via sensors. The safety experts have already implemented several safety applications in their own company in accordance with newly introduced ISO standards. Here, the safety controller (AXC F XT SPLC 1000), which can be added on to the left, supplements the PLCnext Control with the safety-relevant aspects. The safe PLC extension significantly reduces the wiring effort between the safe and the non-safe PLC. The support of the Profisafe protocol also simplifies the integration of safe sensors.
A Safe-Motion-Monitoring library opens up further optimization potential in the future. It enables the user of PLCnext Technology control technology to monitor the motion of the drives in a highly dynamic manner and independently of the sensor/actuator periphery. The universally usable software function blocks were developed in accordance with IEC 61508 and cover important safety sub-functions in compliance with DIN EN 61800-5-2.
Security: Protection against cyber attacks
Since it was clear that AGV units would play an increasingly important role in the production environment in the future, the project team paid particular attention to the issue of security. After all, the failure of an automated guided vehicle system as a result of cyber attacks can massively disrupt logistics processes. The PLCnext Control, TÜV certified against cyber-attacks according to IEC 62443-4-1 ML3 and IEC 62443-4-2 SL2, secures the AGV. In addition, services that are not required – for example, the OPC UA server – are switched off in the control system. Furthermore, the firewall in the controller is activated for remote access.
Navigation: The Robot Operation System
Perhaps the most challenging task of an automated guided vehicle system is path planning and navigation to a specific destination. This requires precise localization for material transfers – even in dynamic work environments. Proprietary solutions proved to be simple but expensive to integrate into the vehicle. PLCnext Technology is an alternative, as it includes various data interfaces (MQTT, REST, OPC UA) to communicate with systems. Another option is the integration of third-party localization solutions into the central control unit – here, the openness of the ecosystem comes into its own once again.
With PLCnext Control, the user receives a controller with an implemented container engine and a wide range of options – such as running the Robot Operation System (ROS) on the PLCnext Control. The ROS (open source) provides numerous tools and functions for the development of a navigation solution, allowing developers to work independently of proprietary solutions. The open source idea is steadily gaining popularity in the industry, which is why Phoenix Contact makes these concepts available.
In this case, a modifiable interface takes over the interaction between the conventional IEC61131 and the ROS environment and makes the data accessible on both sides. This interface was developed together with the Fraunhofer Institute for Manufacturing Engineering and Automation Stuttgart. The PLCnext Technology ROS(2) bridge simplifies data exchange. In addition, configuration options are offered for various use cases. Apart from the classic approach of controller and industrial PC, the powerful PLCnext Control can be used as uniform compact solutions. This reduces the integration effort of additional systems.
Electrification: Maximum reliability as a goal
In an AGV, energy, data and signals must be reliably distributed. The confined space also requires a space-saving wiring concept. Phoenix Contact’s in-house, coordinated product portfolio lent itself to precisely these challenges: From terminal blocks to preassembled cables, industrial connectors and relays to switches, it was possible to access in-house material.
Communication: Integration into the WLAN infrastructure
The FL WLAN 1010 radio module is installed for communication with the higher-level fleet management system. The device is designed for robust use in the driverless transport system. Since the FL WLAN 1010 supports the WLAN 802.11 a, b, g and n standard, the radio module can be easily integrated into the existing WLAN infrastructure. The device includes a REST interface that is coupled via function blocks in the controller. The parameterization information for the WLAN network is thus located in the PLCnext Control and is transferred to the radio module via REST when required – for example, during initial commissioning. During AGV operation, the controller cyclically reads out the Received Signal Strength Indication (RSSI) and monitors and logs it. In this way, losses in radio communication can be detected in good time before transmission losses disrupt the operation of the AGV.
Energy: Monitor battery and status
Decisive for the availability and efficiency of a vehicle is the battery management. The AGV project uses inductive charging technology, which enables simple integration and management of charging. In-house DC/DC converters reliably provide the 24 V voltage for the electronic components. Similar to the drives, commissioning as well as evaluation of the data is PLCnext-controlled via the CAN protocol. With the web server integrated in the PLCnext Control, users interact with the AGV – via smartphone or tablet PC. There they can see information from the control system, such as battery status, error messages, operating time and other vehicle data. The HTML5 pages for this were created with the PLCnext Engineer software tool. In the engineering system, the user projects both the control program and the safety program for the safety controller. The data is also available for visualization via the web server.
Conclusion
Phoenix Contact has gained valuable and, above all, positive experience in setting up and using the automated guided vehicle system in the Blomberg production facility. This project know-how adds another product innovation to the solution portfolio: efficient and safer AGVs for production supply. The necessary components and systems are available in-house, both the hardware and the software – based on the open control platform PLCnext Technology. The broad product range in the area of power, signal and data distribution makes it possible to develop new dedicated and innovative components and systems for automated guided vehicles.
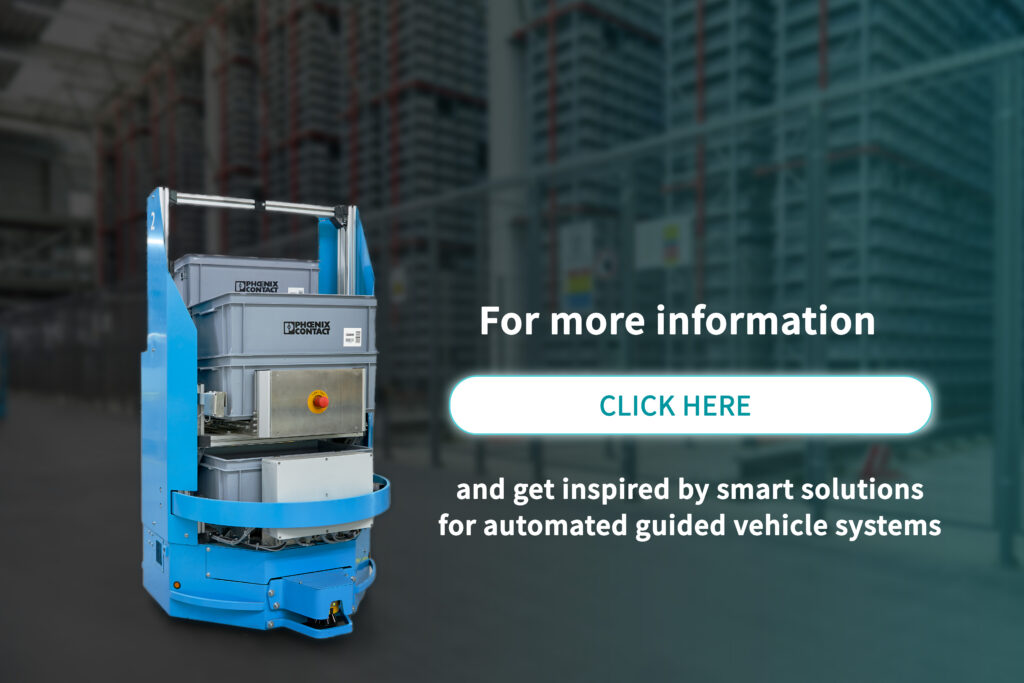