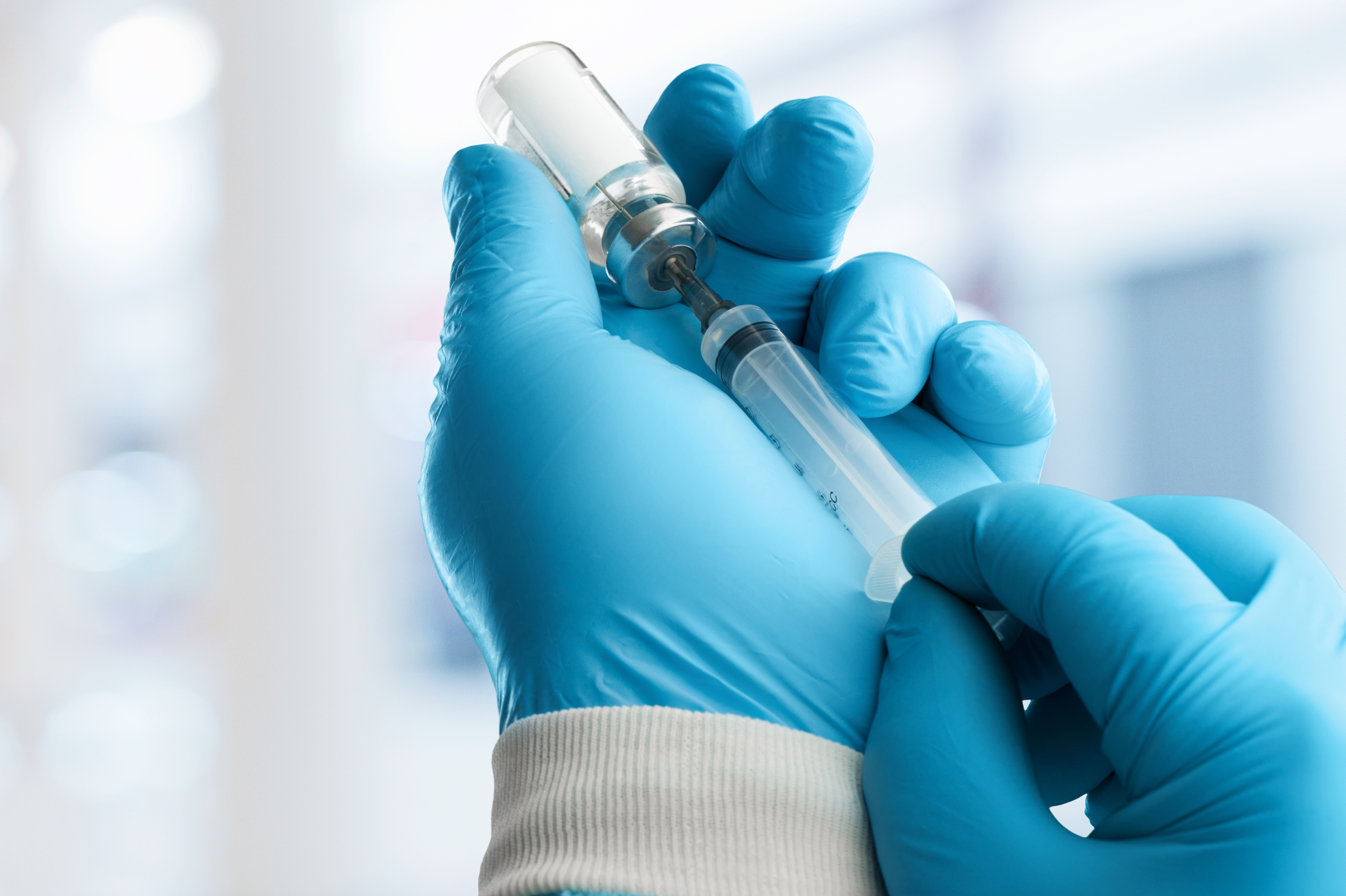
A look into one of the largest vaccine manufacturer Serum Institute of India in Pune
Answers for existing and energy-intensive brownfield factories
Companies are under enormous pressure today – customers and legal requirements demand more sustainability, while competitive pressure forces them to be more efficient. Digitalization is the key – but how can it be implemented in ongoing operations, in old plants and without causing security risks or productivity losses? With Digital Factory now Phoenix Contact provides answers to today’s customer digitalization challenges especially for existing and energy-intensive brownfield factories. Regardless of where the customer stands today, the solutions cover digitalization needs at all stages of the value chain – leading to the goal of improving sustainability, increasing productivity… but securely.
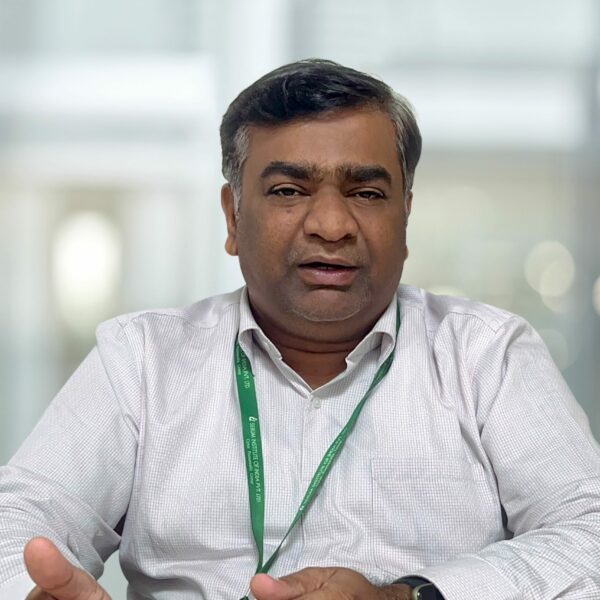
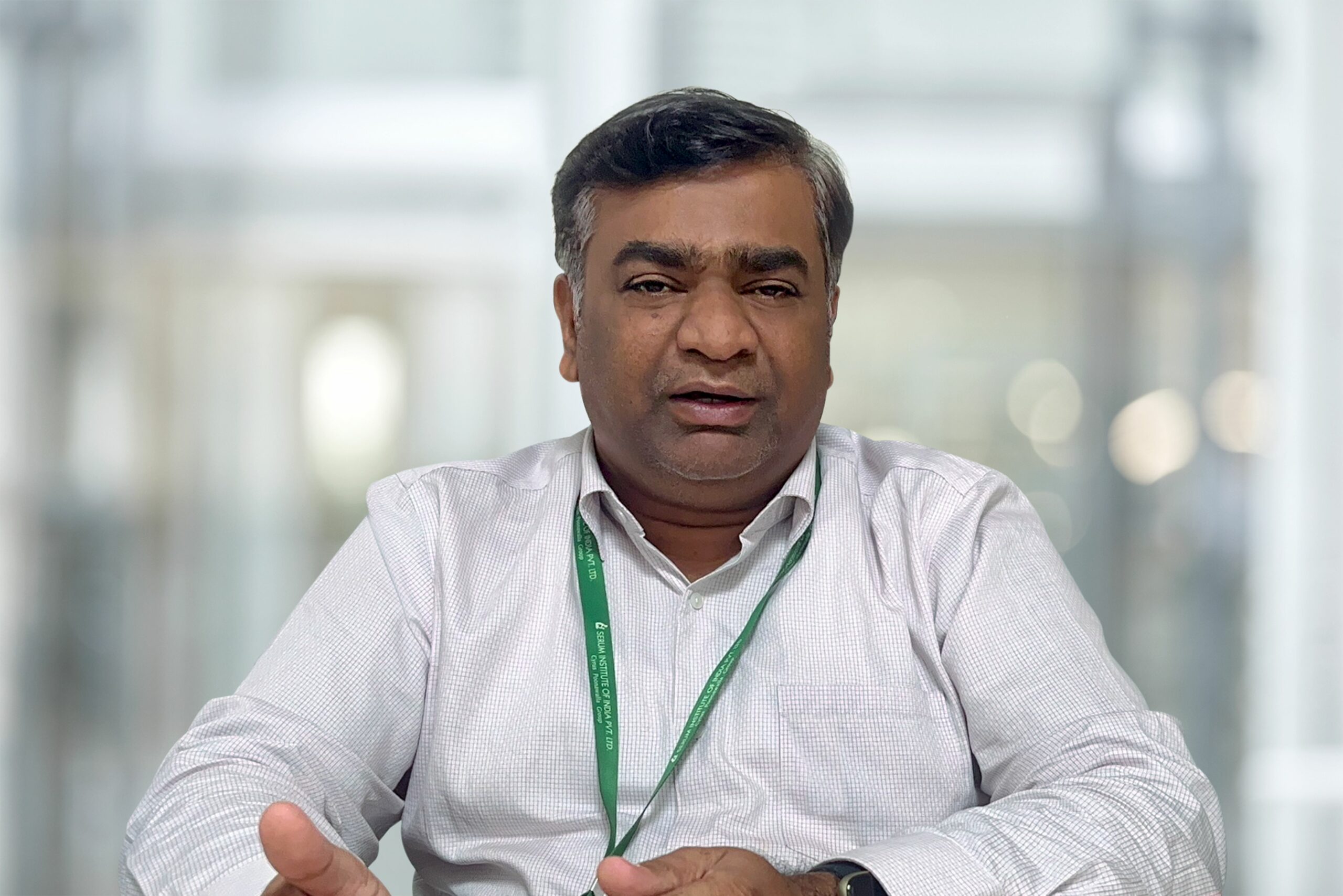
“The openness of PLCnext Technology made it easily possible to securely connect OT and IT and to operate various interfaces. Now we can not only produce more efficiently and thus more sustainably, we also protect our IP.”
Mr. Vishal Patil General Manager IT & Automation
Serum Institute of India
The two major challenges of today are sustainability and digitalization
What looks like a contradiction at first glance, meshes perfectly at second glance. Digitalization is the key to sustainable production. The basis is provided by data. This data must be collected and evaluated to achieve the highest possible level of transparency regarding consumption and processes. This is the first step towards increased sustainability. Only those who know where their resources are being used can develop levers to minimize this consumption and optimize processes. On the way to greater sustainability, productivity is also increased as a side effect. Digitalization is the cornerstone for securing competitiveness in the long term.
But while the requirement and the associated benefits are largely clear, most of our customers are overburdened with the actual introduction and implementation of digitalization. Where to start? What data should be collected? How do I get data from existing machines, plants, skids and sensors? How do I create a continuous data transport, from OT to IT? How well is my factory protected against cyber-attacks?
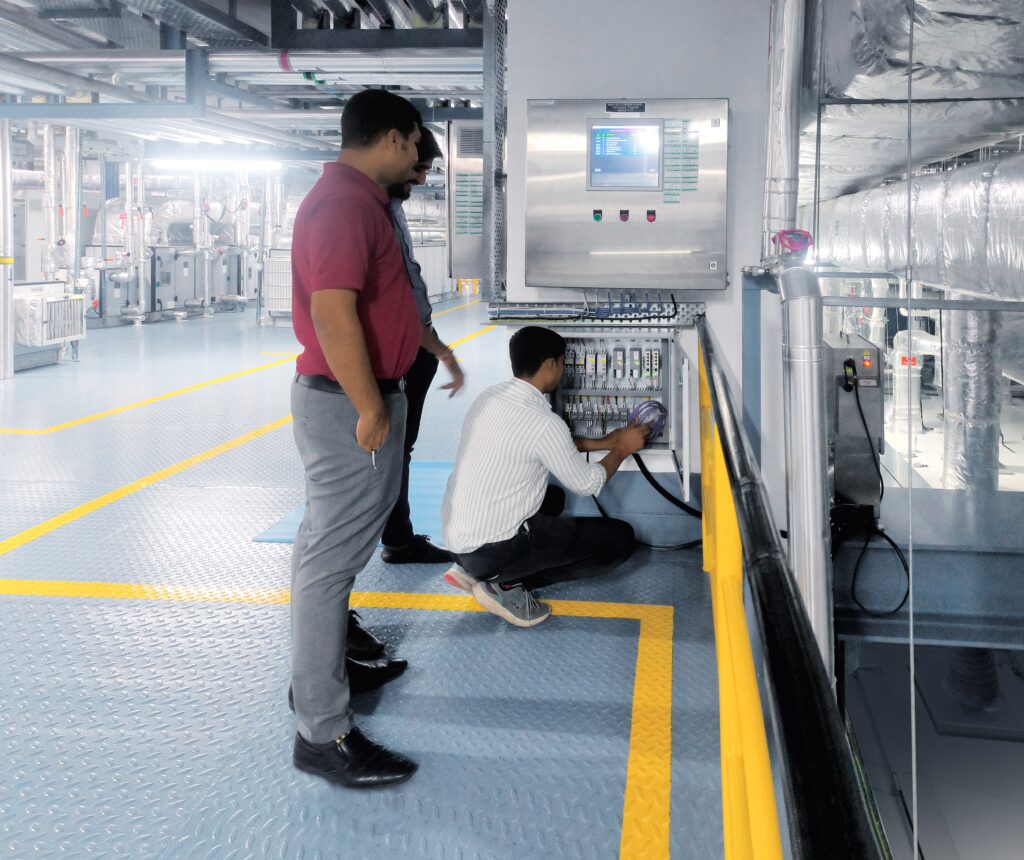
With the Serum Institute of India, one of the biggest vaccine manufacturers in the world, and the close collaboration with the system integrator Control and Automation, we realized three main objectives within the project:
- Golden batch: To achieve the lowest possible deviations from the golden batch all relevant processes must be monitored and evaluated. Complete data transparency is designed to ensure the quality of vaccines and efficient processes to improve sustainability by avoiding waste and wastage of valuable resources.
- Predictive maintenance: To be able to meet promised vaccine deliveries and to avoid expensive, resource-intensive idle times, it is important to prevent system failures under all circumstances. Process transparency and anomaly detection help to detect and eliminate emerging defects, e.g., due to material fatigue, before they even occur.
- Security: Protecting IP to the outside world while preventing tampering is paramount in such an industrial environment.
The Serum Institute of India wanted to implement a CDAS (Central Data Archival Systems) system. Therefore, the customer approached Phoenix Contact with the task of collecting and storing data from more than 300 machines and processes in their existing plant and making it available to the SCADA system. The challenge here was a multitude of different communication protocols and the connection of OT with IT. Phoenix Contact’s Data Collection Box solution made it possible to collect the desired data from the existing plants without jeopardizing certifications or ongoing operations. The IIoT-Framework as an open and scalable interface, normalizes the very different data and enables a “translation” for the customer’s existing SCADA system and thus connects OT and IT. However, a major advantage of the Phoenix Contact solution was the openness of PLCnext Technology, which made it possible to operate the many interfaces, which would not have been possible with a proprietary system. In addition to data collection and processing, convinced the customer with its comprehensive security know-how and certified high-quality products according to IEC 62443 that enable convenient handling of data from inside and outside the company, but at the same time ensure state-of-the-art security in every aspect.
Major advantages of the solution
- Collect, store and visualize data from more than 300 machines and processes and make them available to the SCADA system
- 60% reduced engineering time during the installation
- State-of-the-art IEC 62443-certified security that enables convenient data handling
Find out more about the Digital Factory now!
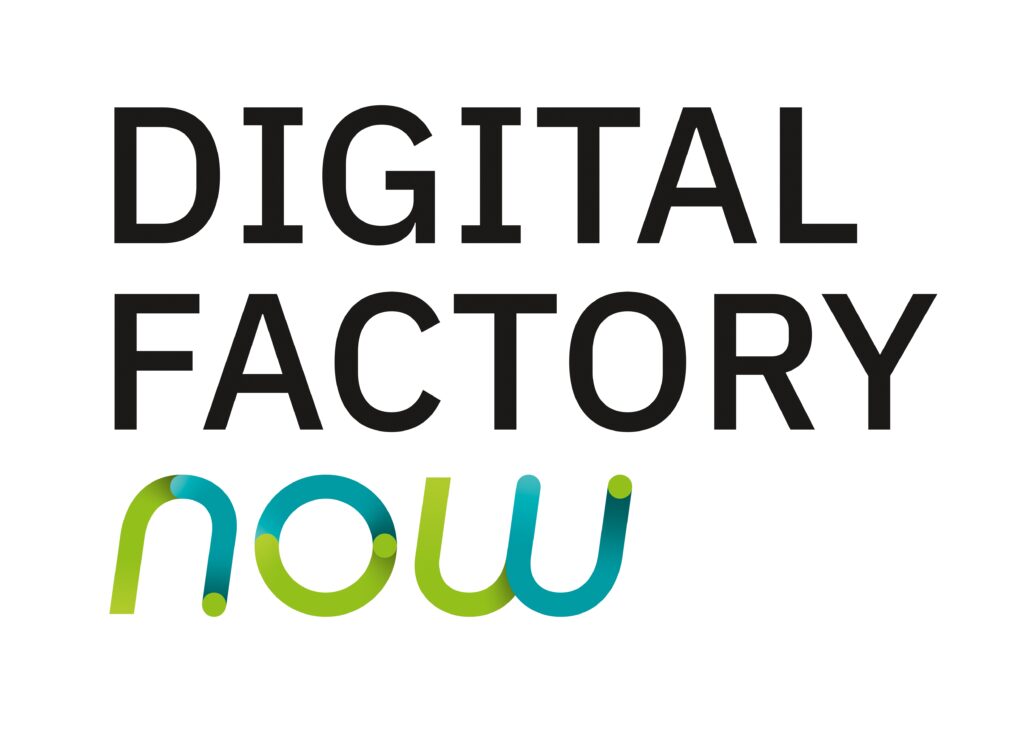