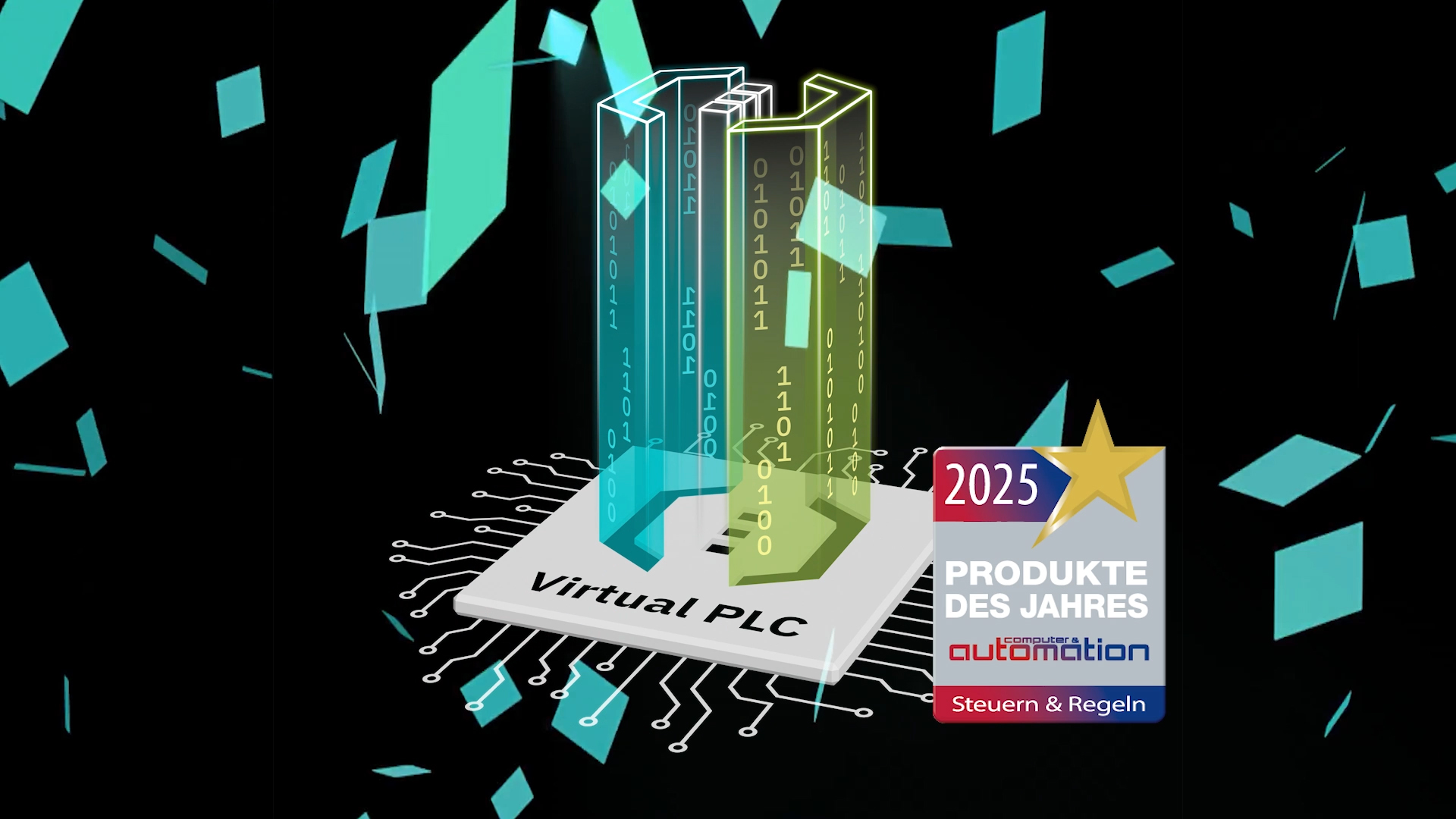
We have great news to share! Our Virtual PLCnext Control has been awarded Product of the Year 2025 in the “Control” category by the renowned magazine “Computer & Automation.”
This is a huge success, and we are incredibly proud of it!
What is Computer & Automation?
For those who may not know, “Computer & Automation” is a leading trade magazine in the field of automation technology. Every year, it publishes around 600 products and selects the best ones in various categories. The readers of the magazine then have the opportunity to vote for their favorites. This year, nearly 5600 valid questionnaires decided that our Virtual PLCnext Control deserved first place in the “Control & Regulation” category.
Why is Virtual PLCnext Control so special?
Our Virtual PLCnext Control offer more scalability, flexibility and cost efficiency in automation. As software in an OCI container, they enable seamless integration, combine OT and IT security and increase the hardware independence of your control solution.
Here are some reasons why it stands out:
- Cost Efficiency: By using multiple virtual controls on a single hardware platform, procurement costs can be reduced and new controllers can be implemented quickly without additional hardware costs. This approach minimizes investment costs and allows for rapid deployment of new control systems.
- Flexibility and Scalability: Controllers can be easily adapted and extended to meet new requirements. Resources such as CPU cores, RAM, and network interfaces are scalable. Applications can be seamlessly moved from one hardware to another thanks to container technology, ensuring adaptability and growth.
- Ease of Maintenance: Maintenance and updates can be carried out easily using proven IT administration mechanisms. The use of containers simplifies management and deployment, reducing downtime and ensuring that systems remain up-to-date with minimal effort.
- Cybersecurity: The combination of IT and OT security measures provides comprehensive protection. The isolated operation of the virtual controls in the container minimizes the risk of security vulnerabilities, ensuring that industrial systems are secure and resilient against cyber threats.
- Energy Efficiency: By consolidating hardware, energy consumption can be reduced, offering a sustainable solution. This approach not only lowers operational costs but also contributes to environmental sustainability by reducing the overall energy footprint.
- Future-Proofing: The system architecture is based on the open ecosystem PLCnext Technology, ensuring a high degree of adaptability and expansion capability. This guarantees that you are equipped for future developments and technologies.
- IT/OT Convergence: The seamless integration of IT and OT enables more efficient networking and control of data and processes. This convergence allows for better decision-making and optimization of industrial operations, bridging the gap between information technology and operational technology
Flexibility and Scalability Made Easy
Virtual PLCnext Control enables increasing convergence of IT and OT, as well as higher flexibility and scalability of automation solutions. It is based on the functions of the established PLCnext Control and expands the PLCnext Technology portfolio. Our open ecosystem allows the combination of automation tasks and IoT requirements in one device. Apart from the control hardware, the ecosystem includes the modular software platform PLCnext Engineer, the digital marketplace PLCnext Store, the informative PLCnext Community for professional exchange, and the option of systemic cloud integration.
Running on Software Alone
Virtual PLCnext Control runs on an OCI container (Open Container Initiative), meaning it operates solely on software. It supports well-known container management tools and standard protocols like PROFINET and ModBus. Multiple virtual controls can run on a single server, further increasing efficiency and flexibility.
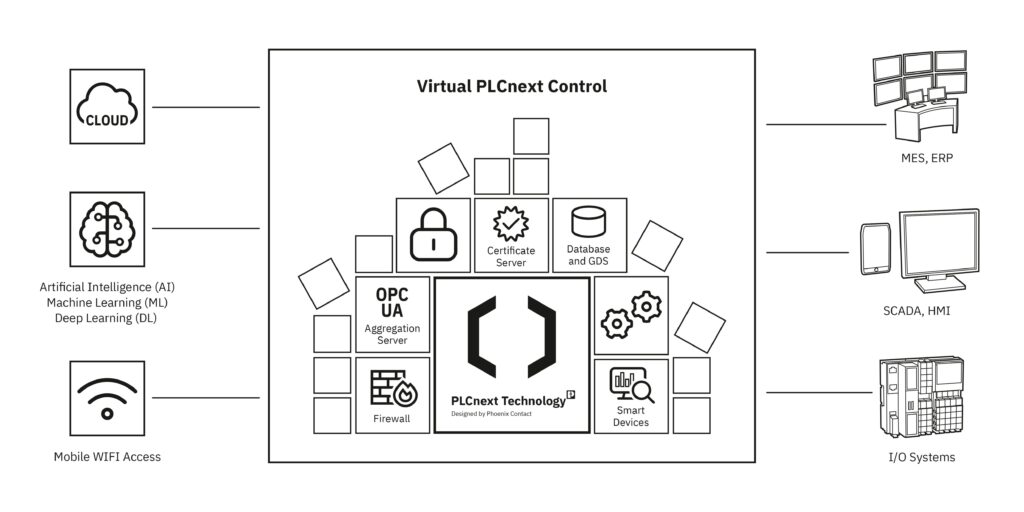
Thanks to container technology and the resulting increasing hardware independence, Virtual PLCnext Control can benefit directly from the interfaces, functions, and performance of the target hardware. For example, connection to the system network via Wi-Fi and deep learning by using the target hardware performance are possible. Furthermore, Virtual PLCnext Control provides familiar functions from the PLCnext Control world, such as the firewall, the certificate server, fieldbus connections, and even database functions. OPC UA and PROFINET can be used to communicate with the SCADA and control system as well as with the I/O fieldbus level.
Adaptable to Your Needs
Virtual PLCnext Control is optimally suited for modern IT environments and facilitates easy migration between classic and virtual PLCnext controls. It allows for quick commissioning and updates, as software solutions can be deployed more easily. This makes Virtual PLCnext Control particularly well-suited for applications requiring high flexibility and scalability. Whether handling a small project or a large installation, Virtual PLCnext Control adapts to specific requirements and ensures smooth operation.
With Virtual PLCnext Control, we offer a solution that not only meets the demands of today’s automation world but also opens up forward-looking possibilities. And the best part? Our users agree! This award confirms their trust and our continuous efforts to develop solutions that truly help our customers achieve their goals.
Want to get more information about Virtual PLCnext Control? Head over to our blog article on Virtual PLCnext Control for all the details or visit our website.
Twice as nice
Did you know that not only has our Virtual PLCnext Control been recognized for its exceptional flexibility and scalability, but our NearFi couplers have also been awarded Product of the Year 2025 in the “Communication & Networking” category by “Computer & Automation”?
NearFi is the contactless real-time transmission technology from Phoenix Contact. It offers flexible application options for any Ethernet protocol and enables power (up to 100 W) and real-time Ethernet data (100 Mbps, full duplex) to be transmitted across an air gap of a few centimeters. NearFi works through gaps such as glass, plastic, or wood and is fully plug-and-play capable, making it easy to replace wear-prone connectors or slip rings in industrial applications.
Read more about our NearFi Couplers and discover all the details.
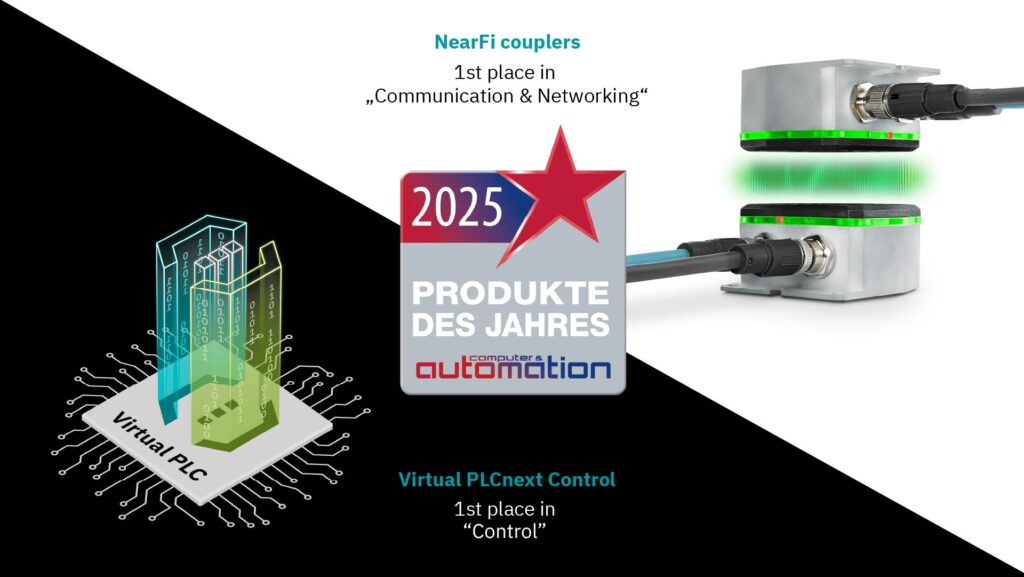