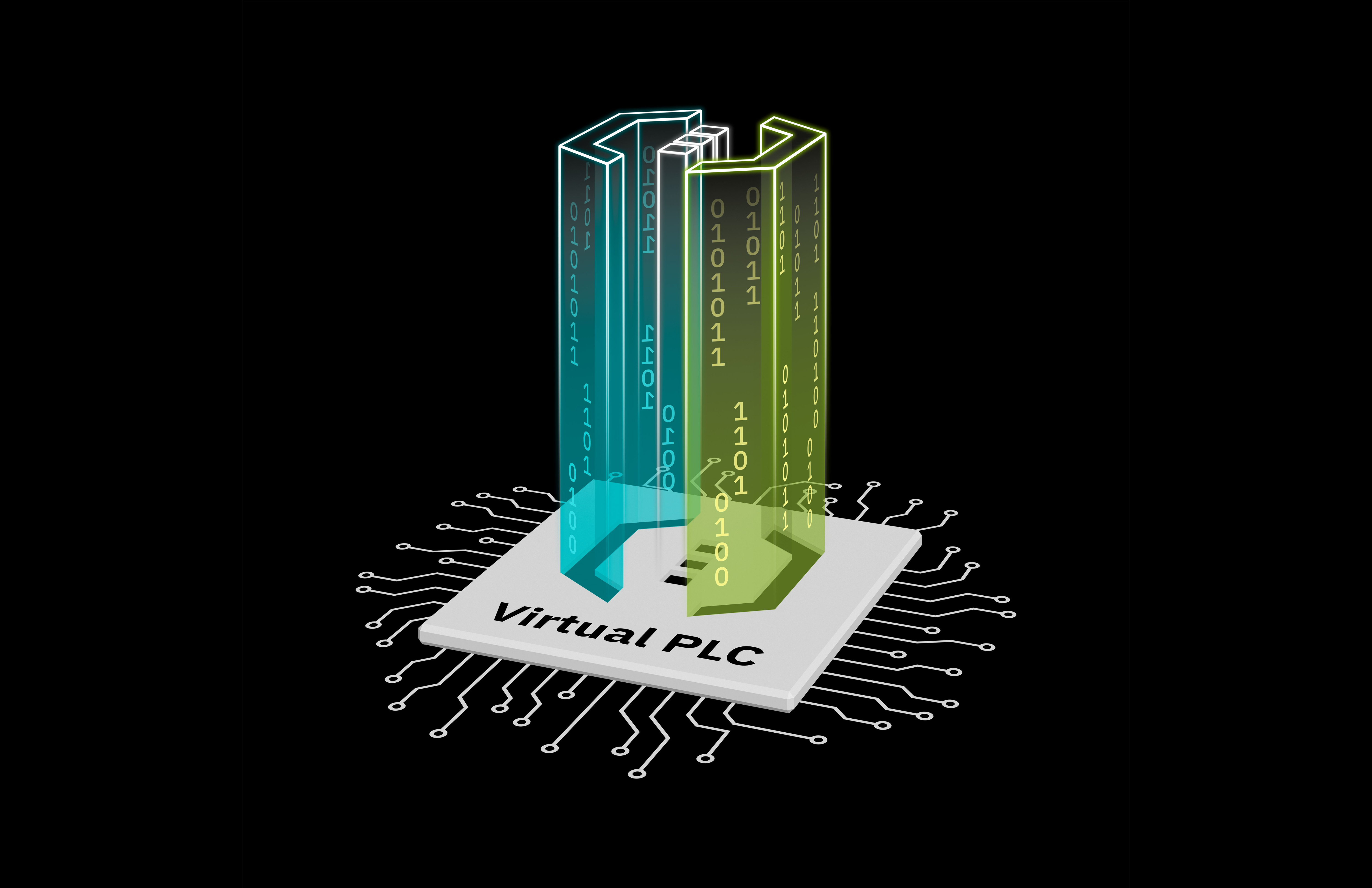
The world of automation is rapidly evolving, and virtualization is at the forefront of this transformation. But can a PLC (Programmable Logic Controller) operate as a virtual device? What are the benefits and potential drawbacks? Discover how flexibility and scalability with Virtual PLCnext Control can enhance automation.
The rise of virtualization in automation
Virtualization isn’t a new concept. It first emerged in the 1960s with mainframe computers and has since become a staple in many industries. Phoenix Contact has harnessed this technology to develop a virtual industrial controller, enhancing the convergence of IT (Information Technology) and OT (Operational Technology) and offering greater flexibility and scalability in automation solutions. The Virtual PLCnext Control builds on the established PLCnext Control functions, expanding the PLCnext Technology portfolio.
Virtual PLCnext Control: A software-only solution
Unlike traditional PLC hardware, the Virtual PLCnext Control operates on an OCI (Open Container Initiative) container, making it entirely software-based and hardware-independent. This means it can be installed on industrial PCs or edge devices, allowing users to create optimized processes without isolating the controller from other processes. The virtual controller retains all the familiar functions of a PLCnext Control, supporting industry protocols and fieldbus systems like Profinet and Modbus TCP/IP for integrating bus couplers and I/O modules into automation solutions.
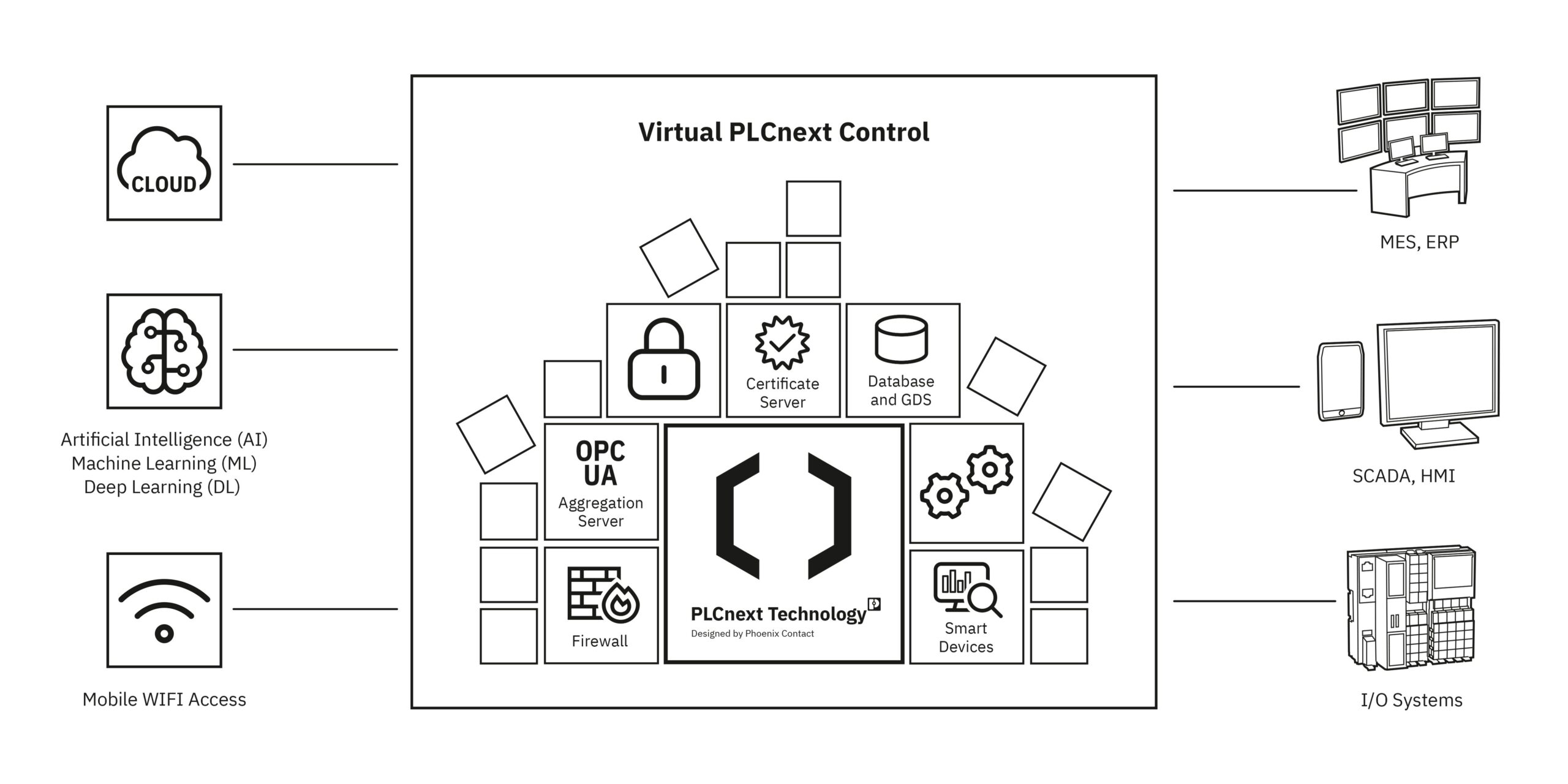
Enhancing traditional PLC hardware
The Virtual PLCnext Control stands out for its flexibility. It can be implemented directly on existing Linux server structures or industrial PCs. Parameters such as Profinet update rates and the number of connected Profinet devices can be freely configured to suit specific applications cost-effectively. But can a virtual controller reliably manage critical production facilities? Absolutely. Traditional PLC hardware essentially consists of industrial PC components, and the shift from hardware to software doesn’t compromise automation reliability. In large or unconventional applications, where data needs to be collected and processed locally (edge applications), the virtual controller is particularly advantageous.
A platform for edge devices
A traditional automation solution can now be implemented with either classic PLC hardware or a virtual controller on existing structures or an industrial PC. The concept of “Edge” refers to the use and evaluation of local data, a process traditionally separated from automation. Virtualizing control functions bridges the gap between IT and OT, allowing familiar operating systems to filter and analyze applications or utilize AI algorithms, thereby generating added value from local data.
Starter kit: VL3 UPC 2440
To introduce the first virtual control, Phoenix Contact will unveil the VL3 UPC Edge in summer 2025. This compact industrial PC combines the benefits of an edge device with a pre-installed container running a Virtual PLCnext Control, ready for immediate automation solutions. Data collection occurs in the familiar IEC 61131 environment, with subsequent analysis performed in the Linux environment using all available software extensions and PLCnext Technology Apps. This solution, while not hardware-independent like purchasing a PLCnext Technology container, offers significant advantages in terms of expandability and user-friendliness compared to traditional, minimalist control systems.
Convergence of IT and OT
The Virtual PLCnext Control brings IT and OT worlds closer together in manufacturing companies. Engineering and programming remain unchanged, allowing the control component to be cost-optimized and precisely configured for its intended use. IT-oriented users also benefit from familiar environments, eliminating the need for adjustments. An open control system like PLCnext Control has long enabled the installation of additional software or apps. Now, with hardware-independent control, users can employ familiar operating systems with easy support for all interfaces, making significant strides in edge applications where OT tools collect and locally evaluate data.
Virtualizing control is a forward-looking approach, especially beneficial in large installations. Instead of installing an oversized PLC to cover all potential future expansions, the container can be precisely adapted to new requirements as applications evolve.
Are you interested in learning more about the entire PLCnext Ecosystem? Feel invited to join our PLCnext Community and connect with many outstanding personalities in the automation world.
Here you will find more information about the Virtual PLCnext Control.